By John McInerny | January 17, 2024 0 Comments
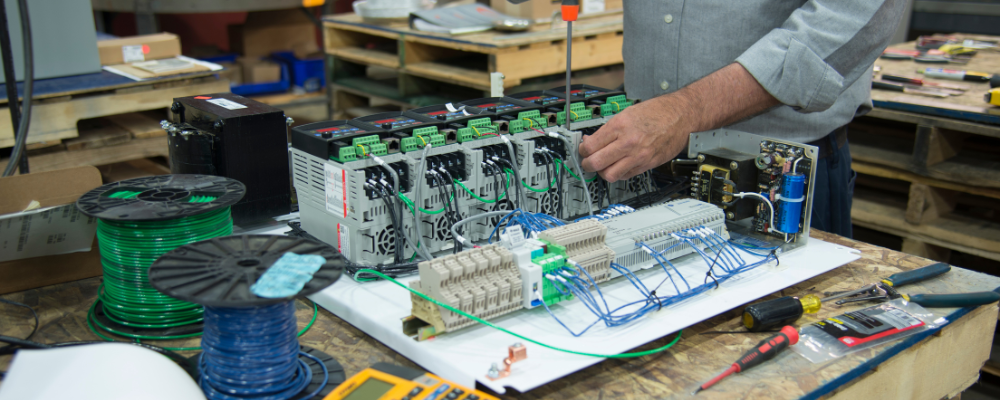
Unpacking Success: The Essential Guide to Packaging Equipment Parts and Service
In the fast-paced world of modern business, packaging isn't just about enclosing products. It's a statement of quality, an assurance of safety, and a safeguard against the perils of logistics and distribution. For many operations managers and business owners, the efficiency and reliability of their packaging equipment can mean the difference between a streamlined process and a costly delay.
This guide will lead you through the intricacies of packaging equipment — the vital workhorses that bring your products to market — and the often-overlooked but critical piece of the puzzle: parts and service. Whether your organization is a bustling e-commerce center or a traditional brick-and-mortar store, the knowledge gleaned from this blog will fortify your approach to ensuring that every package tells a positive story about your brand.
Understanding Packaging Equipment
From Pallet Wrappers to Conveyors
RTU, FFS, and VFFS are not just alphabet soup — they stand for 'Ready-to-Use,' 'Form, Fill, and Seal,' and 'Vertical Form, Fill, and Seal,' respectively. This breadth of packaging equipment types showcases the variety available to modern businesses. When discussing parts and services, each of these machines comes with specific components that are essential for daily operations.
What's less well-known is that these components, sometimes the unsung heroes of the packaging line, require regular upkeep for optimal performance. Packaging equipment can range from the simple to the sophisticated, with different demands on maintenance determined by the technology and capacity.
The Critical Role of Parts and Service
A pallet wrapper with a frayed film carriage, or a conveyor with a hitch in its belt, can bring production to a standstill. The impact on operational efficiency and the domino effect on the entire logistics schedule cannot be understated. Savvy business owners understand that the initial investment in packaging equipment should be followed with a commitment to its ongoing care and maintenance.
Benefits of Quality Parts and Service
The ROI on parts and services is more than just a number — it's a direct reflection of the commitment to excellence that a business espouses. Long-term benefits include increased productivity, cost savings through proactive maintenance, and the extension of equipment lifespan.
Increased Productivity and Efficiency
The speed of modern commerce is relentless, and packaging equipment that maintains high uptime is a competitive advantage. With responsive parts and service support, businesses can prevent issues before they occur, ensuring that every package makes it through the line without a hitch.
Cost Savings and Reduced Downtime
Routine maintenance can identify areas of concern long before they manifest into an operational emergency, saving not only on potential repair costs but also on the hidden expenditure of unproductive downtime.
Extending Equipment Lifespan
The endurance of packaging equipment is directly proportional to the care and attention afforded by a robust parts and service program. Every additional year of service life translates into deferred capital expenditure and increased return on investment.
Choosing the Right Parts and Service Provider
The decision on who to entrust with your packaging equipment's maintenance and repairs is a significant one. The provider must align with your business's values and operational needs, offering not just technical expertise, but also reliability and cost-effectiveness.
Technical Expertise
Look for providers with a proven track record of working with your type of packaging equipment. Vendor-certified specialists bring knowledge born from experience, allowing for swift and accurate issue diagnosis and resolution.
Reliability
Timely intervention is crucial. Ensure your provider has a reputation for responsiveness and that they understand the critical nature of your timeline.
Cost-Effectiveness
The balance between cost and service quality is delicate but achievable. By choosing a provider with transparent pricing and a commitment to excellence, you're investing in the sustainability and growth of your business.
Best Practices for Maintaining Packaging Equipment
With the right provider secured, it's time to enact best practices in the maintenance of your packaging equipment.
Regular Inspections and Maintenance Routines
Adhere to a regular preventive maintenance schedule of equipment inspections, factoring in manufacturer recommendations and the volume of work passing through your packaging line and partnering with someone like Rapid Packaging that offers a customized Preventive Maintenance Plan, designed to ensure your operations never miss a beat. This approach to preventive maintenance stands on the pillars of personalization, comprehensiveness, and responsiveness, reflecting a commitment to your business's continuity and success. Build your customized plan here!
Training Staff on Equipment Usage and Care
A well-informed team can be your eyes and ears on the ground, catching issues before they have a chance to escalate. Training ensures that they understand and follow the best operational procedures, mitigating the risk of misuse and damage.
Conclusion
In business, success is a sum of parts, each playing an equally vital role. Packaging equipment may seem like an independent part of the whole, working silently to support your business's logistics. However, it's the careful attention to the health of these pieces, through a comprehensive parts and service program, that's the hallmark of a well-oiled and successful operation.
Take the knowledge you've gained here and apply it to your business. Invest in your packaging equipment, so it continues to invest in you. The road to reliability is paved with quality parts and service — and it's a road worth traveling for the peace of mind it offers in the rush to meet customer demand and exceed expectations.
If you have any questions in determining your best options for parts and services for your equipment, don't hesitate to reach out. Speak to a packaging automation expert today!
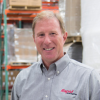
About the Author: John McInerny
Blog Categories
Need Help?
Increase your productivity with entry-level of full-line packaging automation, reduce packaging costs, and increase product protection with a full catalog of packaging supplies.