By Jay Anderson | April 04, 2023 0 Comments
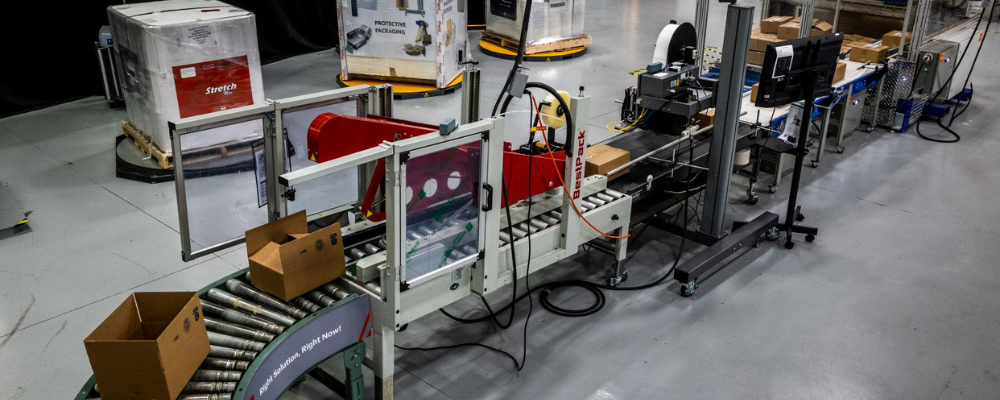
Revolutionizing the Production Line with Advanced Automated Packing Systems
In today's fast-paced business environment, companies need innovative solutions to increase operational efficiency and improve manufacturing processes. With advanced automated packing systems, businesses seek to revolutionize their production lines while ensuring product quality and reducing labor costs. In this blog, we will explore the benefits of implementing these cutting-edge packaging systems, highlighting their significance in manufacturing and the impact they have on the industry as a whole.
Enhancing Productivity and Efficiency
One of the main benefits of advanced automated packing systems is their ability to boost productivity and efficiency on the production line. These systems streamline processes, automate repetitive tasks, and reduce the time spent on manual labor. Consequently, companies can maximize their output, maintain consistent quality, and minimize production downtime. Moreover, advanced automated packing systems can be integrated with existing manufacturing equipment, accelerating the return on investment.
Minimizing Labor Costs and Errors
Implementing advanced automated packing systems allows companies to reduce their reliance on manual labor significantly. Businesses can mitigate labor costs and minimize the risk of human error by automating tasks such as product packing, labeling, and sealing. In addition to this, automated systems enable companies to operate 24/7 without the need for additional workers. As a result, these systems not only enhance productivity but also help manufacturers remain competitive in today's rapidly evolving market.
Ensuring Consistent Quality and Compliance
Advanced automated packing systems can significantly contribute to maintaining consistent product quality across the production line. Precise robotic workstations, inspection cameras, and cutting-edge sensors ensure that packaging tasks adhere to strict quality control standards. This high degree of precision minimizes the risk of product contamination or damage, boosting customer satisfaction and brand reputation. Furthermore, these advanced systems can help companies comply with industry regulations and standards, ensuring the highest levels of safety for end-users.
Scalability and Flexibility
One significant advantage of advanced automated packing systems is their capacity for scalability and flexibility. As a company's production needs grow, these packaging systems can be easily scaled to accommodate increased output levels. Additionally, these systems can be configured for various product lines or packing requirements, providing businesses with a high level of flexibility when updating or modifying their manufacturing process.
Data Analytics and Product Tracking
Some automated packing systems offer comprehensive data analytics and product tracking capabilities. This enables businesses to analyze their production process in real time, identify bottlenecks, and optimize their production line. By incorporating advanced technologies such as Artificial Intelligence (AI) and Machine Learning (ML), these systems can analyze and predict equipment performance, enabling proactive maintenance and minimizing disruptions. Ultimately, this results in improved operational efficiency and long-term cost savings.
Implementing advanced automated packing systems on the production line has become an essential strategy for companies seeking to thrive in today's competitive landscape. These cutting-edge systems revolutionize manufacturing processes and yield significant operational improvements by enhancing productivity, minimizing labor costs, ensuring consistent quality, and providing scalability and flexibility. As industries embrace automation and digitization, advanced automated packing systems will remain vital for businesses' future success and growth.
Thanks for reading!
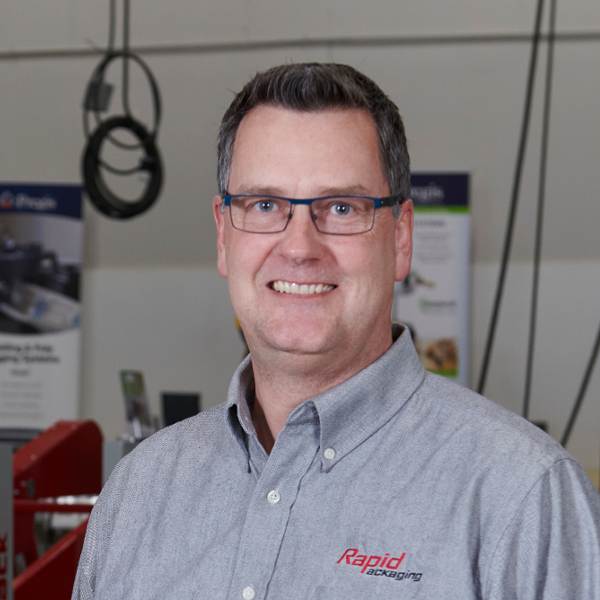
About the Author: Jay Anderson
Blog Categories
Need Help?
Increase your productivity with entry-level of full-line packaging automation, reduce packaging costs, and increase product protection with a full catalog of packaging supplies.