By Laura Heinen | March 04, 2024 | Preventative Maintenance | 0 Comments
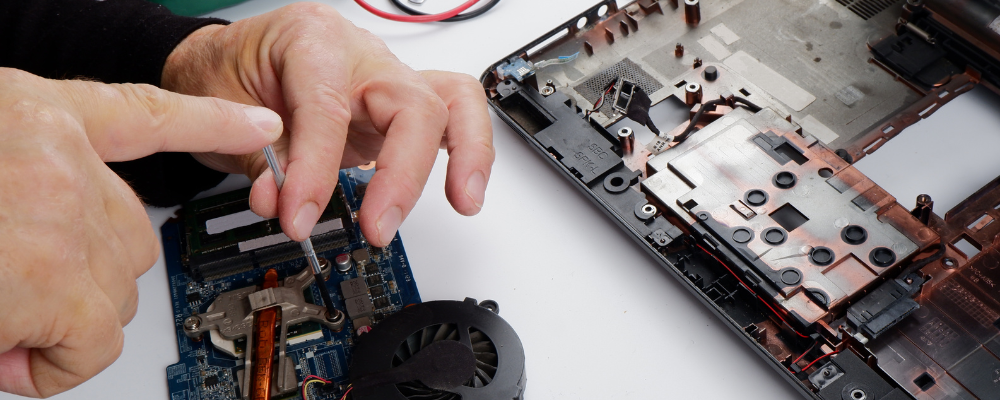
Dispelling Misconceptions About Preventative Maintenance: Unlocking the True Value
In the world of industrial equipment management, preventative maintenance (PM) stands as a cornerstone for ensuring operational efficiency, cost-effectiveness, and prolonged asset lifespan. Despite its proven benefits, myths about preventative maintenance persist, deterring many businesses from embracing this proactive approach. Let's delve into these misconceptions and unveil the truth behind them.
Myth 1: Preventative Maintenance Is Too Expensive. Truth: Contrary to popular belief, investing in a preventative maintenance plan is highly cost-effective. Consider this: one hour of equipment downtime due to unexpected failures can potentially exceed the annual cost of your PM plan. By proactively addressing issues before they escalate, you mitigate the risk of costly repairs and production losses.
Moreover, preventative maintenance helps in avoiding emergency breakdowns, which often require expensive parts and specialized labor. With a well-designed PM program, you can budget and plan for maintenance activities, preventing unexpected financial burdens. Additionally, by optimizing equipment performance, PM reduces energy consumption and operational costs in the long run, contributing to significant savings.
Myth 2: Preventative Maintenance Is Time-Consuming. Truth: Scheduled maintenance, far from being a time sink, is a strategic time-saver. Research reveals that planned maintenance can slash machine downtime by a significant margin, ranging from 30% to 50%. By adhering to a well-structured PM schedule, you streamline operations, enhance productivity, and minimize disruptions.
Moreover, proactive maintenance allows for better planning and scheduling of maintenance activities. By allocating resources efficiently, you can optimize the use of labor and minimize the impact on production schedules. Ultimately, this leads to smoother operations and increased throughput. Additionally, modern technologies such as predictive maintenance software enable predictive analytics, further reducing downtime by anticipating equipment failures before they occur.
Myth 3: Preventative Maintenance Is Unnecessary. Truth: Every piece of equipment, regardless of its complexity, requires regular maintenance to ensure optimal performance and longevity. Preventative maintenance isn't merely an option; it's a necessity for safeguarding your critical assets and maximizing operational efficiency. Neglecting PM leaves your equipment vulnerable to unforeseen breakdowns, costly repairs, and compromised productivity.
Preventative maintenance helps in identifying potential issues before they escalate into major problems. By conducting regular inspections and addressing minor issues promptly, you can prevent costly breakdowns and extend the lifespan of your equipment. Moreover, proactive maintenance ensures that your equipment operates at peak performance, maximizing efficiency and reducing energy consumption.
Understanding the misconceptions surrounding preventative maintenance is crucial, but it's equally essential to grasp its significance. A robust PM program encompasses various tasks, including routine inspections, lubrication, calibration, and component replacements, tailored to the specific needs of your equipment.
Implementing a preventive maintenance plan involves strategic planning, meticulous scheduling, and leveraging advanced technologies like preventive maintenance software. By embracing preventive maintenance, you not only mitigate the risk of equipment failures but also unlock a myriad of benefits, including:
- Reduced Downtime: Proactive maintenance minimizes unplanned downtime, ensuring uninterrupted operations and smoother production workflows.
- Cost Savings: By addressing issues preemptively, you mitigate the need for costly emergency repairs and extend the lifespan of your equipment.
- Enhanced Safety: Regular maintenance reduces the likelihood of workplace accidents, promoting a safer working environment for your employees.
- Improved Efficiency: Well-maintained equipment operates more efficiently, consuming less energy and yielding higher output with minimal wastage.
- Regulatory Compliance: Adhering to a comprehensive PM program helps ensure compliance with industry regulations and standards, safeguarding your business reputation and avoiding potential penalties.
At Rapid Packaging, we understand the pivotal role of preventative maintenance in optimizing operational performance and reducing costly repairs. Our experienced professionals specialize in helping businesses create tailored PM programs that align with their unique requirements and operational objectives.
Ready to debunk preventative maintenance myths and unlock its full potential for your business? Reach out to Rapid Packaging today to speak with one of our knowledgeable experts. Visit our website at https://www.rapidpackaging.com/ for more information and to schedule a consultation. Let's embark on a journey towards enhanced efficiency, reduced downtime, and sustainable success together.
Contact Us Today to Learn More About Preventative Maintenance Plans!

About the Author: Laura Heinen
Laura is the sales and marketing manager for Rapid Packaging. She earned her Bachelor of Science in Business Management with an emphasis in Marketing from the Minnesota School of Business. .
Before becoming the sales manager, Laura's main passion focused mainly on Marketing because it allows her to speak to the world, and if she does her job well enough, the world will speak back.
Laura lives in the twin cities suburbs and is a mom of two girls. In her spare time, you can find her cheering on the Vikings or the boat all summer long!
Blog Categories
Need Help?
Increase your productivity with entry-level of full-line packaging automation, reduce packaging costs, and increase product protection with a full catalog of packaging supplies.