By Billy Soule | April 07, 2022 0 Comments
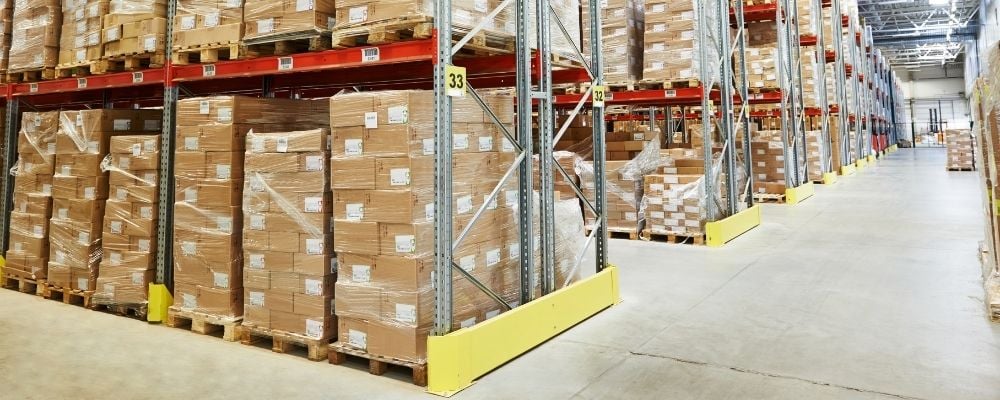
How End-of-Line Packaging Can Increase Your Bottom Line with Local Inventory
In the modern world, you can't be a success if you don't take advantage of every opportunity. That's why it's so important to invest in your end-of-line packaging. When done right, end-of-line packaging can help increase efficiency and effectiveness with local inventory by reducing shipping costs, getting the product to the customer faster, and improving customer satisfaction.
In order to make the most of your end-of-line packaging, it's important to use local inventory. This will ensure that you're able to get the product to the customer faster and improve customer satisfaction. Additionally, using local inventory can help reduce shipping costs, making your bottom line even more impressive.
What is End-of-Line Packaging
End-of-line packaging is the process of final packaging and preparation of a product for shipment. This can include anything from adding labels and stickers to the product to boxing it up and preparing it for transport. In many cases, end-of-line packaging is done in a warehouse or other storage facility near the customer.
Why is it Important to Use Local Inventory in Your End-of-Line Packaging
When it comes to end-of-line packaging, using local inventory can be extremely beneficial. By using local inventory, you'll be able to reduce shipping costs, get the product to the customer faster, being strategic with your warehouse space and improve customer satisfaction. Additionally, using local inventory can help improve your bottom line.
Shipping Costs
One of the biggest benefits of using local inventory in your end-of-line packaging is the reduction in shipping costs. When you use local inventory, you'll be able to avoid the cost of shipping the product from a distant warehouse. This can save you a lot of money and improve your bottom line.
Faster Delivery
Another benefit of using local inventory is faster delivery with increasing customer demand. When you use local inventory, the product will be delivered to the customer faster than if it were shipped from a distant warehouse. This can improve customer satisfaction and help your business succeed.
Be Strategic with Valuable Warehouse Space
To maximize the value of your warehousing space, warehouse managers can be strategic about how they use your space. With access to local inventory, you can be in more direct control over when you want to have your products available in your building, avoid running out, and have less excess inventory on your floor.
Improved Customer Satisfaction
Finally, using local inventory can improve customer satisfaction. When the product is delivered quickly and without incident, the customer is more likely to be happy with the purchase. This can lead to repeat business and a stronger bottom line, and overall keeping your customer base happy!
If you're serious about your business, it's important to take advantage of every opportunity. One way to do that is by investing in end-of-line packaging with local inventory. Local inventory can reduce shipping costs and improve customer satisfaction while also helping your bottom line. When used correctly, this type of end-of-line packaging will help increase your efficiency and effectiveness, and improve your customer experience.
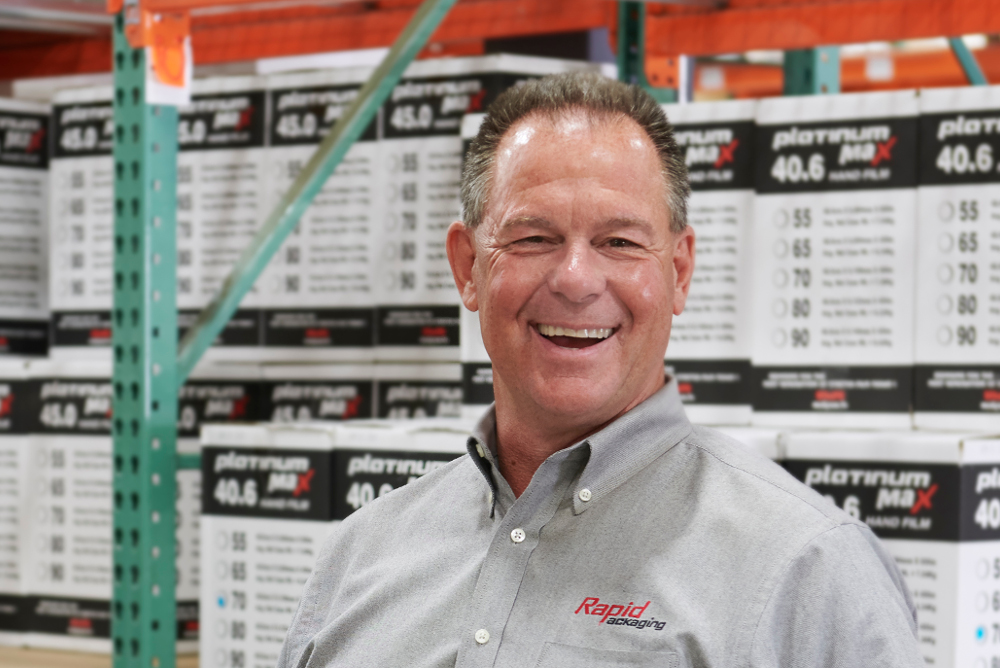
About the Author: Billy Soule
Blog Categories
Need Help?
Increase your productivity with entry-level of full-line packaging automation, reduce packaging costs, and increase product protection with a full catalog of packaging supplies.